Hybrid load introduction structure [1]
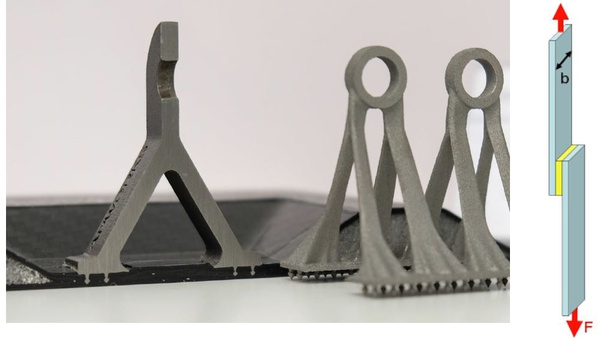
Fiber-reinforced plastics (FRP) are increasingly being used in modern aerospace structures due to their excellent weight-specific mechanical properties. As a result, the development of optimal joining techniques for FRP components is becoming increasingly important. Metal-FRP connections are increasingly being used, particularly in the area of load introduction. The loads are introduced into the FRP component via metallic components (bearings, fittings), as shown in Figure 1, for example. The metallic components can be manufactured using additive manufacturing with optimized topologies. It is also possible to print pins for the joining area, which are integrated into the FRP component during the joining process (co-curing). In this way, an extremely effective hybrid connection for load transfer can be realized.
Current research work is concerned with the design of pin-reinforced metal-FRP joints. One design aspect is the optimal arrangement of the pins in the joining area for the most effective load transfer possible. In this thesis, an optimization of the pin arrangement is to be carried out using the example of a single-lap joint (Figure 2). For this purpose, a finite element model of the single lap joint is first to be set up and parameterized. By varying the pin arrangement, the joint is then to be optimized with regard to maximum specific stiffness.
[1] APWORKS (2020) Hyperjoint: additive metal + composites = stronger, tougher joints. CompositesWorld