2.5-Dimensional pressure of a rotationally symmetric component into space
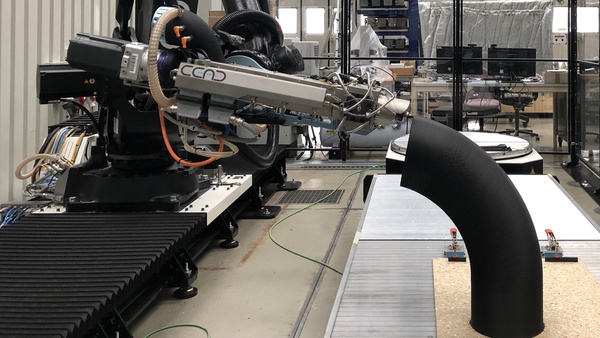
In recent years, large-scale additive manufacturing systems have become increasingly popular in industrial and scientific fields. Especially for polymer and composite materials, the material extrusion (MEX) process, which is characterized by a simple process control, is applied [1].
Analogous to additive processes used elsewhere, such as selective laser sintering (SLS), the component properties of the desired end product depend on various factors. These include the complex thermal history induced by the process and the resulting microstructural processes [2]. Especially in the case of semi-crystalline thermoplastics, processes occur at the material level that can have both a positive and a negative influence on the macrostructural component properties. One negative influence is, for example, the thermal residual stresses that occur as a result of crystallization and cause shrinkage of the component. Furthermore, crystalline structures, especially at the junction of two extrudate strands, can hinder the diffusion of molecular chains and thus reduce adhesion. The consequence is an anisotropic material behavior in the final product [3].
In order to be able to counteract the above-mentioned challenges, the processes occurring at the material level are to be described and investigated. The project focuses on the development and validation of a detailed simulation model to represent the MEX process and the material modeling of the thermal crystallization, which is to be integrated into the simulation [4]. Furthermore, in addition to variations of various manufacturing parameters, additional peripherals, including heating and cooling elements, are to be used to modify the temperature field in the running process [3].
The macrostructural component characteristics are to be derived and determined from the numerical findings obtained. Furthermore, potential sources of error in the large-scale MEX process can be represented in advance, thus saving time and material costs.
Simulative representation of the MEX - process
Microstructural investigations with respect to thermal crystallization
Macrostructural investigations
Demonstrator
The knowledge gained in this research project will be used to minimize potential defects during the manufacturing process and to predict the component properties of the final product. The focus will be on the investigation of microstructural processes, here in the context of crystallization. The results obtained should provide users of large-scale MEX systems with greater certainty in the design of components and the correct choice of manufacturing parameters.
Furthermore, a process improvement by means of additional peripherals shall be achieved or investigated. The heating and cooling elements used in this process are to be used to selectively adjust desired component properties, in addition to the choice of manufacturing parameters. The printing and realization of components with suitable component properties in actual three-dimensional space is to be achieved in the long term.
In summary, this basic research serves to increase mechanical component properties of the end products and to improve the manufacturing process.
This research work is funded by dtec.bw – Digitalization and Technology Research Center of the Bundeswehr which we gratefully acknowledge [project FLAB-3Dprint]. dtec.bw is funded by the European Union – NextGenerationEU.