Shear distortions in an adhesive layer with structured CFRP joining parts at 400 N (top) and 500 N (bottom). The distribution of the shear distortions is visibly influenced by the structure of the bonded parts.
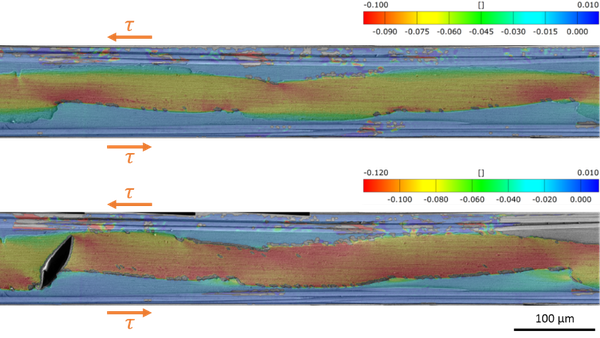
Due to their outstanding lightweight construction properties, fiber-reinforced plastics have become firmly established in modern aircraft construction. Structural bonding is a joining technology that offers considerable advantages for these materials. Adhesive bonded joints generally enable designs with high stiffness combined with low weight. For fiber composites in particular, adhesive bonding allows thinner wall thicknesses and no weakening of the joined parts, a more uniform stress distribution compared to bolted or riveted joints, and good vibration damping. [1]
However, the safe application of load-bearing bonded joints in aerospace is still the subject of current research. A key challenge is to reliably predict the service life and damage behavior of the bonded joint. While ensuring adhesion is already reliably mastered [2], a clear dependence of crack growth in loaded fiber composite bonded joints on the joint topography is evident [3].
In the aerospace industry, material tests are often performed on coupon specimens for process qualification. Due to the size of these specimens, effects in the micrometer range can only be detected superimposed. This is particularly problematic for a material such as CFRP, since it is very inhomogeneous on the microscale. Therefore, a methodology has been developed to perform material testing on a scale where the influence of the microstructure can be captured. For this purpose, miniaturized specimens are fabricated and tested in a material testing machine in a scanning electron microscope. The deformations occurring under load in the adhesive layer and in the area of the bonded parts close to the adhesive layer can thus be recorded on a micrometer scale and subsequently evaluated by means of digital image correlation. In combination with numerical simulations, this enables a better understanding of the micromechanical behavior of the bond.
Investigation of fiber composite bonded joints
Method development for in situ strain measurement on polymers in the micrometer range
Simulation
The project has already demonstrated how the behavior of bonded fiber composites under load can be quantitatively investigated on a micrometer scale.
One focus was on the generation of a stochastically distributed pattern with high contrast in the scanning electron microscope, which is necessary for strain determination using image correlation.
The methodology developed in this study for an experimental investigation of micrometer-scale bonded joints already provides valuable insight into the fracture mechanics in the bonded layer. This allows a systematic investigation of different configurations of bonded parts and adhesives, which contributes to a significant gain in knowledge and a better predictability of the lifetime of bonded joints.
M. Rasche, Handbuch Klebtechnik, München; Wien: Hanser, 2012
J. Holtmannspötter, The Journal of Adhesion Vol. 96:9, p. 839 (2018).
T. Thäsler, J. Holtmannspötter and H.-J. Gudladt, Key Engineering Materials Vol. 809, p. 341 (2019).